Dr Terry Keech’s recent study into the barriers to achieving mass low carbon social housing has highlighted the knock-on effect planning policy can have on the entire supply chain. Here, he explains why
It will come as no surprise to construction professionals that there is an evident gap between intended performance and actual performance of low carbon technologies. However, less explored are the causes of this performance gap.
A recent study therefore analysed the construction process – from the initial planning stage right through to the building contractors who sign off the commissioned installation – to gain a deeper insight into the contributing factors.
Tracing the problem back
A significant finding from the research was a lack of buy-in from the supply chain. In most instances, the low carbon technology selected at the local authority planning stage was specified due to planner’s preference, expediency of assessment or simply cost; rarely for the benefit of the development.
The findings showed many contractors felt that local authorities did not always have the technical know-how to properly consider the most appropriate technology for a given development, with many just “ticking boxes” to meet their obligations.
“Local authorities have limited understanding really and truthfully what they need to do they’re just not interested, they have to tick a box.” – Contractor.
“I think there’s a lot of things that are getting through planning on a lip service basis rather than because things have been properly considered in the spirit of what the planning requirements are all about.” – Contractor.
When the chosen technology is then ‘forced’ on to the design and build contractor, there is a disconnection from the outset. This ‘tick-box’ approach results in a lack of buy-in at build stage, which causes issues that then filter down and implicate the whole project.
For example, the study showed that when a main contractor has limited knowledge of the low carbon technology chosen, they commonly defer responsibility to subcontractors and then take little or no interest in the quality of the installation.
Consequently, subcontractors are appointed to ensure ‘successful delivery’ and not ‘successful performance’. For those subcontractors whose tender bids are higher than other competitors – to ensure ‘successful performance’ – the chances of their success are greatly reduced.
In fact, the study revealed that 67% of contractors and 83% of designers agreed that monitoring installation is the least common activity undertaken on site. It is this ‘blind trust’ given to the subcontractor (or disinterest) that is another contributory factor to the performance gap.
The current EPC process does nothing to counter this. With certifications awarded on theoretical modelling and inadequate legislation to ensure effective commissioning, the reported Dwelling Emission Rates (DER) and Target Emission Rates (TER) very rarely correlate with the real performance levels of the property.
Only 29% of those questioned thought commissioning was carried out effectively on site, with 68% believing that the commissioning process was not fit for purpose. And while this appears to be common knowledge within the industry, there seems to be no desire to challenge the status quo.
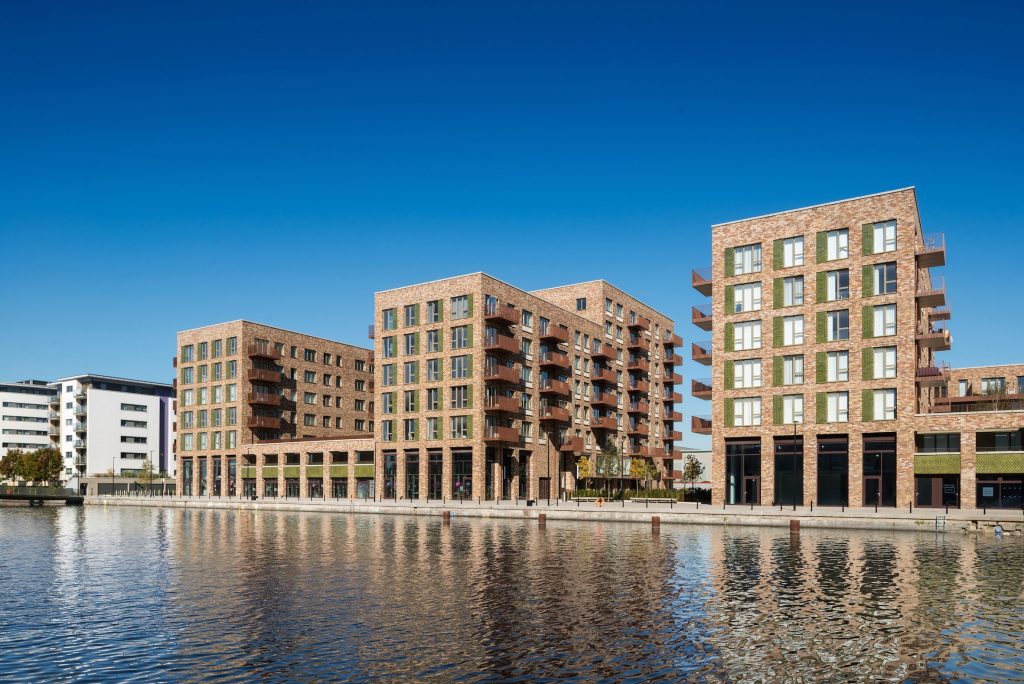
Bridging the gap
Evidently, there needs to be a fundamental change to ensure the gap between ‘intended performance’ and ‘actual performance’ of low carbon technologies is bridged.
One route to recovery is to start from the very beginning – at the planning stage. The key to this stage is identifying a focus with a “sense of commitment” (McNiff et al 1996). The ‘actual performance’ should be made a mandatory standard that can be tested, and, more importantly, validated.
From a practical perspective, a recommended intervention is a Commission2Perform template, a new process of reporting installation and commissioning activities. Central to the process is a single point document that logs a clear and concise set of information on activities throughout the construction process, which can both complement and support the O&M manual.
To support this process, the following documents would be included in a central document:
- List of installation drawings/schematics with revision and date.
- Electronic issue of all ‘as installed’ drawings.
- Commissioning programme with revisions.
- Commissioning certificate list.
- Defects record for the defects period.
This could form part of Building Control, with a development’s adoption of the required level of renewable technologies only signed off when it can be proved that the technology has been properly installed and commissioned.
There is no silver bullet that will solve the looming performance gap. However, change, even where small and incremental, does have a direct effect on the performance of the technology. Clear performance criteria must be given and enshrined within the contractual process to encourage management, monitoring and quality checks throughout the entire delivery process. This investment in knowledge, commitment and buy-in from the very beginning will help to create a new working practice that will contribute to further change.
To discover more about Commission2Perform, please visit: www.calfordseaden.com
Dr Terry Keech
M&E Engineer and Partner
Calfordseaden
Tel: +44 (0)20 7940 3200
Twitter: @calfordseaden
LinkedIn: Calfordseaden LLP