In this article, find out how Imerso’s AI technology enhanced fire wall construction compliance for the iconic Nyt Hospital Nordsjælland near Copenhagen
Ensuring regulatory fire wall construction compliance is getting a high-tech boost.
Over the past 16 months, the construction team responsible for the iconic new Nyt Hospital Nordsjælland near Copenhagen used Imerso construction AI technology to achieve fire safety compliance.
Using Imerso, the team enhanced work productivity while preventing risks of rework costs and delays worth €5.2m during the construction of the hospital project.
Inspired by this success, the team led by project manager Anders Kaas has since been eager to explore the potential of the technology in other areas.
The opportunity arose to address a topic that traditionally posed significant challenges and expenses in numerous construction projects – ensuring regulatory compliance of fire barriers and fire wall constructions.
Fire safety compliance in the construction industry is growing
In light of recent fire incidents in the UK, fire-protection compliance has surfaced as a pressing concern, coinciding with stricter regulations within the UK construction industry.
Not complying with fire-safety standards can lead to exorbitant repair costs and prevent critical societal projects like hospitals and airports from opening doors to operations entirely.
In Denmark, perhaps the most infamous recent case is that of the landmark Niels Bohr university construction.
The project suffered precisely this fate in late 2021 when final inspections revealed that over 10,000 fire closures had not been done properly. This resulted in the already delayed handover to the University of Copenhagen being postponed indefinitely until all issues were fixed.
The client, Vejdirektoratet’s director of construction Erik Stoklund Larsen commented: “It is extremely frustrating that we have to spend so much effort – and so much time – in the final phase of the project to correct something that should never have been a problem, namely the incorrectly executed fire closures”.
The case prompted the Roads Directorate to carry out additional investigations on other construction projects, specifically targeting the quality of fire wall construction to mitigate the same scenario from happening elsewhere.
Motivated to go further than the norm, the construction team at NHN invested in Imerso’s jobsite supervision AI to monitor construction quality proactively. The opportunity emerged to aim the solution towards reducing fire-safing compliance risks.
What is fire wall construction?
Critical infrastructure buildings like the Nyt Hospital Nordsjælland must adhere to hundreds of fire-safety codes.
Compartmentation and passive fire protection systems like fire barriers, fire-rated walls, fire doors, or fire-stopping filling materials, are fire blocking strategies used in building construction to prevent or stop the spread of fire, smoke, and gases from one area to another.
One of the most renowned challenges in construction concerns fire-safing interfaces between rooms or floors, with openings for technical services installations to pass through. Depending on the context, engineers can use specific fire-blocking solutions such as 2-hour fire-rated walls, which are designed to resist fire for that rated amount of time.
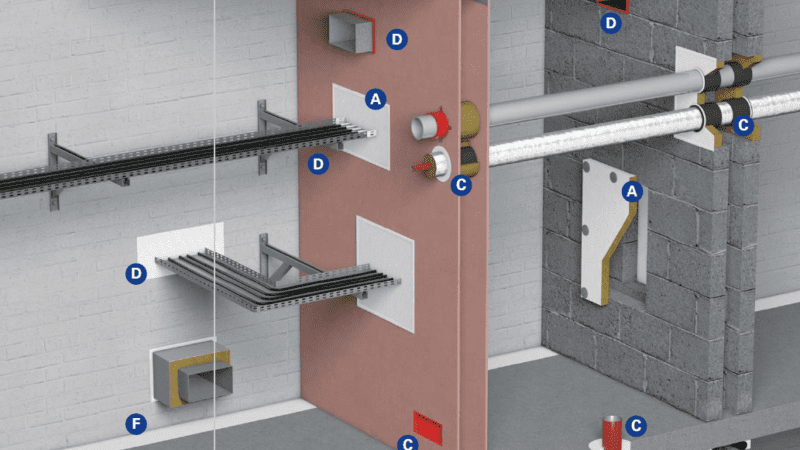
Manufacturers like Knauf test their systems to determine their performance and get an official fire-rating score. However, the performance of the system is entirely dependent upon its assembly exactly as prescribed.
Unless the firestop systems are installed according to the manufacturer’s instructions, the fire rating will be compromised as there is no guarantee the system will perform as intended.
Observing these requirements is especially vital in complex projects like the Nyt Hospital Nordsjælland, featuring multiple operating rooms packed with radiation-shielded walls, layers of interwoven technical equipment, and strict fire-stopping regulations.
What are the common challenges in fire wall construction compliance?
Within 3 months of targeting Imerso towards fire-rated wall installations, the system already placed a variety of potential issues on Anders’ radar so the team could prevent these from becoming a problem.
A common example is the case of Fire Section walls and Fire Cell walls, where metal stud framings must be placed at minimum distances from each other and without modification, to preserve the intended fire rating.
A major challenge is that after the installation of the metal studs of fire partition walls, subsequent teams struggle to install planned technical equipment across the walls, often leading them to cut the metal studs to make space and thereby compromising the fire rating of the wall.
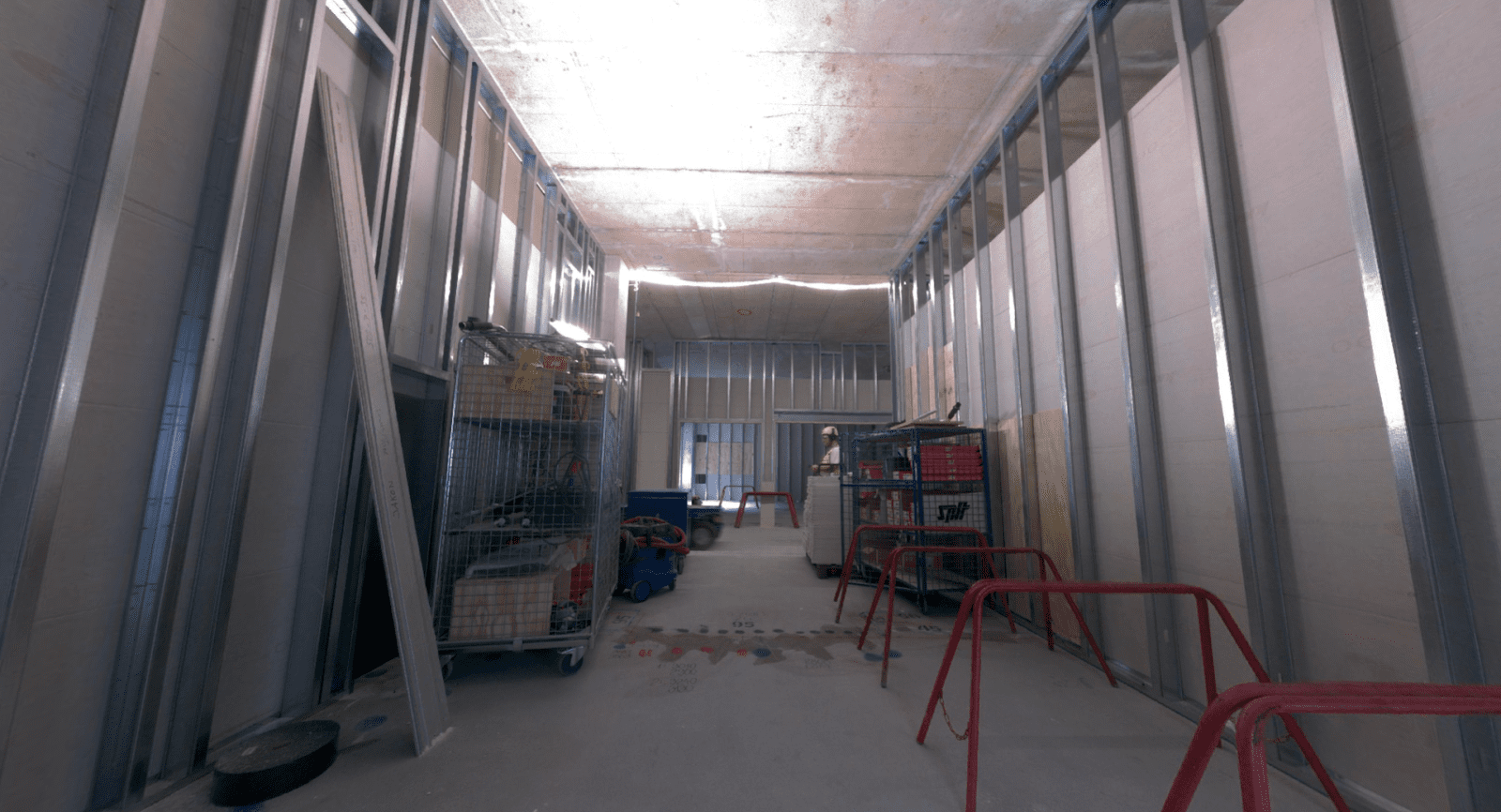
This is a common predicament: On one hand, the precise position of the metal wall studs is typically not modelled in BIM, as these are normally installed in situ to fit the onsite conditions at that time.
On the other hand, the position of technical MEP/HVAC installations is well defined in BIM, and construction teams are instructed to not deviate from those specifications to avoid disciplinary clashes at a later stage.
Sequencing challenges are common during construction
From the designers’ side, the onsite teams are responsible for installing the metal framing properly in accordance with the specifications while observing the layout in the BIM models for technical services.
Installing the fire-rated wall studs requires preparing encasing boxes framing the openings where technical installations of a certain size should go through the wall, complying with the specifications for a propper fire seal.
In contrast, from the onsite teams’ perspective, such a process requires a coordinated planning approach to ensure the layout for technical MEP/HVAC services is agreed upon before partition walls are erected. It is ideal to have the openings prepared prior to the installation of technical services.
However, doing this requires the service layouts to be accurately overlaid on the partition drawings in advance. This is rarely done. Design teams are often still optimising layouts during the coordination phase, and even small changes to the layout of the services will affect the placement of the metal wall studs.
This sequencing challenge is a major risk for the project. As Anders explains, “The problem typically happens when fire partition walls are closed from both sides, and you can no longer see the inside. Let’s say the MEP installer arrives later with a drill to work on the installation: it can happen that the wall studs are damaged and thereby compromise the fire integrity of the wall.”
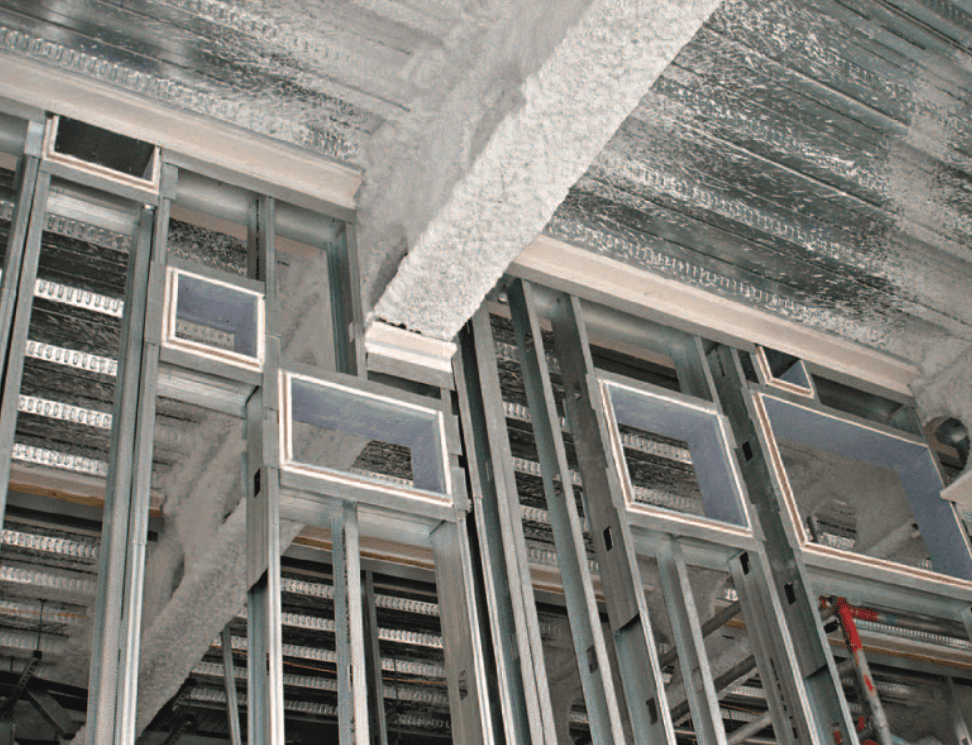
Checking work quality of fire rated wall installations with Imerso AI
Imerso enabled the construction management team at Nyt Hospital Nordsjælland to boost their site supervision ability 15-fold. This was achieved by enabling the team to take over 3D Scanning activities at the jobsite entirely by themselves as a daily routine – a task historically regarded as too time-consuming and requiring expert surveyor resources or costly third-party services.
The Imerso platform continuously analyses the As-built environment onsite against the project’s BIM models automatically, immediately reporting on work status and any problematic deviations so these can be addressed early.
This enabled project manager Anders Kaas and his team to prevent hundreds of costly issues within months, vastly surpassing their expectations for the technology. Read about the first 16 months’ results here.
Anders’s team can easily monitor the installation of fire-rated wall studs on-site with millimetre precision, by recording the exact placement of metal stud framing in fire partition walls and have Imerso compare it to the current BIM plans.
This lets them rapidly identify any potential issues with planned openings or technical objects that collide with the current placement of metal studs. The team then uses this information to find solutions early and avoid any problems down the line. All of this is done in a matter of minutes, providing an efficient and much more effective way to monitor the work status routinely and ensure the safety of the building.
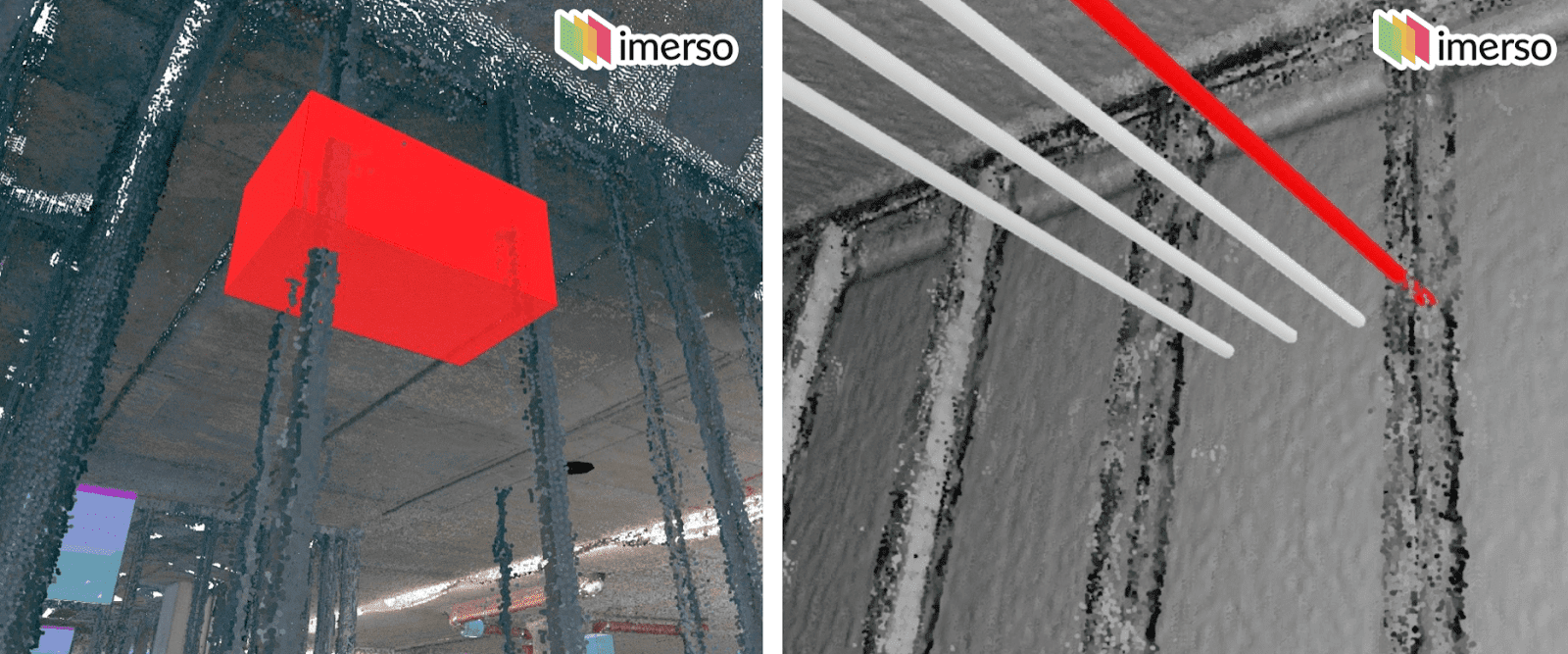
Imerso AI technology helps to detect onsite installation issues
Another typical fire-stopping challenge in construction projects lies in the installation of technical equipment through wall openings in the concrete superstructure. To preserve fire-stopping capabilities, such equipment must be installed at specific distances from the structure and between each other, to allow appropriate fire-rated insulation.
The popular BIM coordination software Solibri, an industry-leading tool and partner of Imerso, recently launched new rulesets for validating fire-safety compliance automatically in the BIM models.
But even in projects leveraging these accurate models, the problem happens when the onsite installations deviate from the planned design and remain undocumented, since traditional manual and visual controls using photos, 360° panorama images, and manual checklists are ineffective at flagging such changes.
By analysing the onsite installation status against the BIM plans, Imerso helps the Nyt Hospital Nordsjælland team to prevent such hidden deviations from being overlooked, by detecting them instantly without human subjectivity.
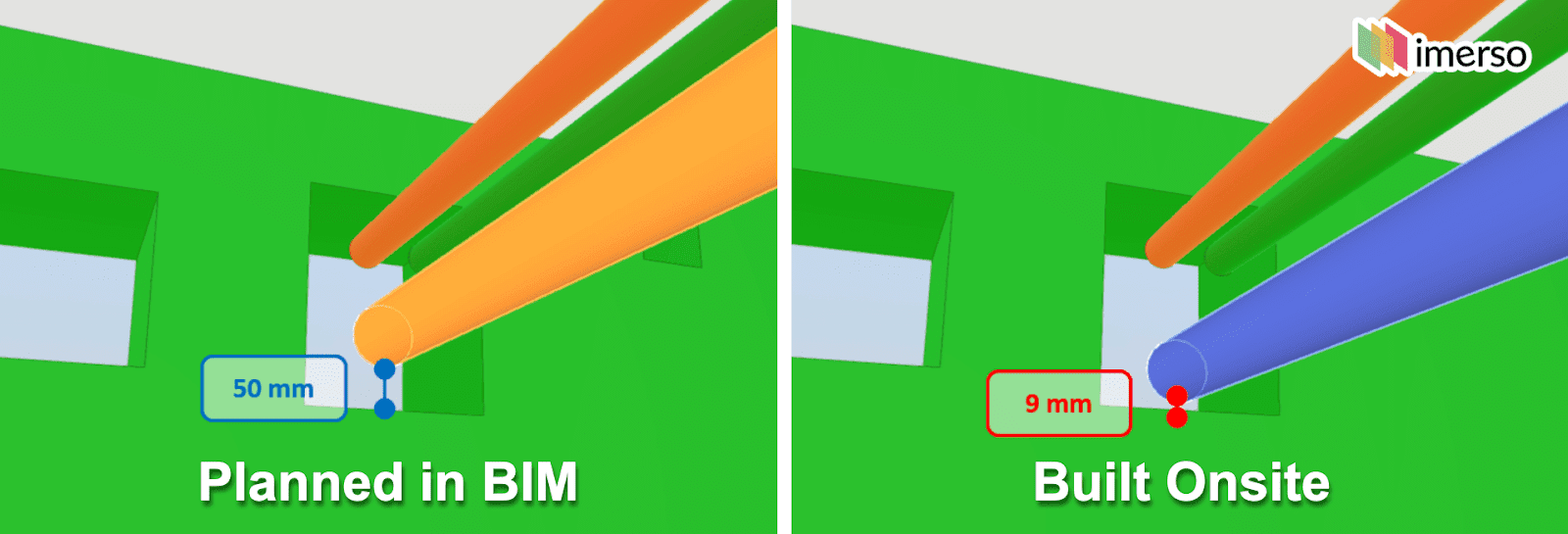
Construction companies need more than new software
The construction of each floor at the Nyt Hospital Nordsjælland project features hundreds of thousands of metal framings in fire-rated walls, making traditional construction control approaches reliant on manual checks, photos or panorama images too subjective and ineffective. This leaves dangerous blind spots in any construction project.
The Nyt Hospital Nordsjælland team estimates that Imerso is helping them monitor 15x times more onsite objects than other approaches, using only 7% of the resources.
Using Imerso AI technology, the team can now prevent problems before they occur by detecting any deviations early and promptly sharing detailed information with the affected teams. Nonetheless, Anders explains that the strategy can only succeed given proper internal adoption and cross-partner collaboration.
According to Anders, “Imerso enables us to surface numerous cases likely to pose a serious threat to the project. This is a much better approach than the traditional way of monitoring work quality, but we are not hoping to present this as the perfect solution so everyone can relax.
“Such risks can never be removed entirely, and no tech product will help if companies resist adapting and try new ways of working. What we need most is to have an active organisation that takes full advantage of this new source of data and puts the right incentives to prioritise work quality in both 3D model coordination and physical installation.”
Imerso has helped Nyt Hospital Nordsjælland to enhance fire wall construction compliance
By dedicating just a few hours of onsite scanning work per week in combination with Imerso, the NHN team has already prevented significant rework costs in fire-rated wall cases.
But Anders underlines that “while avoiding rework costs and delays is great, the construction savings in these cases are a drop in the ocean compared to the big elephant risk: that the hospital cannot open operations entirely because of compliance issues that such cases could bring. That would be an enormous problem both in financial and societal terms. The technology’s impact on reducing this risk is invaluable.”
Construction companies increasingly use automatic work quality monitoring systems like Imerso to verify thousands of fire wall constructions and other installations across their projects.
This is a welcomed reduction in the risk of costly surprises and headaches that have plagued projects for decades.
To learn more, read the fire safety case study on Imerso’s website.