Dr Kwadwo Oti-Sarpong of the Cambridge Centre for Smart Infrastructure & Construction examines the organisational strategies deployed in delivering net zero buildings using manufacturing approaches and digital technologies
The recent government industrial strategy (IS), the Construction Sector Deal, outlines ambitious targets that require the construction sector to deliver, among others, net zero buildings that use very low energy and are built faster and at a lower cost.
Achieving these, the government anticipates, will help reduce construction and whole lifecycle costs by over a third, leading to better value for money and halving delays of construction projects and greenhouse gas emissions by 2030.
For the construction sector to achieve these targets, the IS outlines a transformation strategy that places the use of digital technologies, manufacturing approaches (e.g. offsite manufacturing (OSM)) and early consideration of whole-life asset performance at the forefront.
The government anticipates that the implementation of these strategies for construction project delivery will improve productivity, safety, timely delivery and cost-effectiveness, consequently accruing benefits to clients, contractors and end-users.
The realisation of the targets outlined in the IS needs an active buy-in from construction firms who will execute projects by implementing strategies that enable the use of digital technologies, manufacturing approaches and early consideration of whole lifecycle asset performance.
Although a widescale implementation of all or part of these strategies is desired by the government, uptake among construction firms (e.g. contractors, designers, specialist consultants and suppliers) is generally low for a wide range of economic or commercial, organisational, individual, regulatory and contextual reasons.
Despite the low adoption of the foregoing strategies, promising developments can be observed in the construction sector. Few construction firms have begun devising and implementing project delivery strategies that are manufacturing- and digital technologies-led, alongside early whole-life asset performance considerations.
This article discusses, in brief, the organisational strategy implemented by a design and build contractor (DBC) in delivering net zero buildings for educational and residential purposes in the UK.
Key findings underscore the importance of committed leadership and management, a business strategy that prioritises the use of manufacturing and digital technologies for project delivery, and the development of relevant capabilities. Ensuring continuous cross-project learning and intra-organisational knowledge transfer are also critical elements in an effective organisational strategy.
The organisational strategy of DBC explained
DBC specialises in the delivery of educational net zero buildings but also delivers housing for public and private clients. The overarching organisational strategy developed by DBC establishes a framework that drives the design of all projects in digital environments and their construction using manufacturing approaches and techniques. For every project DBC undertakes, these strategic considerations underpin the go-to methodologies used, which are under constant review and refinement.
DBC’s organisational strategy that guides its project delivery comprises elements of leadership and management, capabilities development, learning and critical skills – all essential ingredients for the successful delivery of projects that are driven by digital and manufacturing innovations. Figure 1 provides a graphical representation of the strategy.
DBC’s vision for carbon emissions reduction
DBS was originally established as a manufacturing firm fabricating steel components for buildings. In recent years, it underwent a transformation and ventured into the delivery of buildings for educational and housing purposes.
Having observed industry trends and taken into consideration the benefits of using manufacturing approaches and digital technologies, the board and management of DBC refocused strategic organisational priorities.
The firm’s leadership is passionate about carbon emissions reduction, applies modern approaches to its business operations as a design and build firm, intends to automate some design and construction processes, and has already driven several changes.
Internal transformation that has taken place under the new leadership includes the implementation of a business strategy making the use of Building Information Modelling (BIM) as the standard design environment for all projects and designing for projects with offsite construction as the main approach for delivery.
Doing so allows DBC to make design decisions (e.g. for concepts, material specifications, component/modular designs and productisation of building elements) while considering whole-life asset performance from the onset and making associated decisions with their clients.
Altogether, these decisions, from a strategic point of view, contribute to the DBC’s vision to become a leader in the niche area of delivering net zero buildings.
Net zero implementation pathways
At DBC, the use of digital technologies for designing, costing and monitoring project execution using BIM software like ARCHICAD, Revit and Cost X alongside modelling and component-based methodologies for delivery is the norm rather than the exception.
As the standard business strategy for delivering projects, DBC endeavours to highlight to its private and public clients the gains they stand to make – with emphasis on energy cost savings.
For its suppliers (e.g. specialist consultants and subcontractors), DBC clarifies – in consultation with the client – project hierarchy and lines of communication in order to ensure that their strategy is implemented with their cooperation.
Learning and knowledge transfer form an essential part of the strategy implementation. The design, manufacturing and on-site assembly teams of DBC emphasise communication, feedback, evaluation and refinement – all integral elements in their learning strategy.
Every project is considered an opportunity to learn within teams, from their supplier network, clients and regulatory framework to integrate new learning points into existing mechanisms underpinning the strategy implementation.
For instance, innovative approaches used in solving a design-based fabrication problem during the manufacturing stage for one school project are passed on from the factory team lead to the design team lead either through an email or an annotated hardcopy drawing for future reference. Such learning, gathered from every project experience, provides suggestions for how the existing business strategy could be improved.
Capabilities and technical skills to deliver net zero projects
The implementation of the strategy at project levels requires the development of internal operational capabilities and interface management competencies. To this end, DBC began its digital transformation journey a little over four years ago in response to the government’s BIM mandate in 2016.
Since then, design professionals have been hired to work on projects using ARCHICAD and Revit for designs and CostX for project costing and budget planning. The manufacturing team, as part of internal capabilities developments, has an interface manager who liaises with the design and on-site assembly teams.
Developing the requisite capabilities to manage the design-manufacturing-construction interfaces, as well as external project partners and supplier networks remains under development.
These areas, the design team leaders identify, are critical and need to be developed quickly.
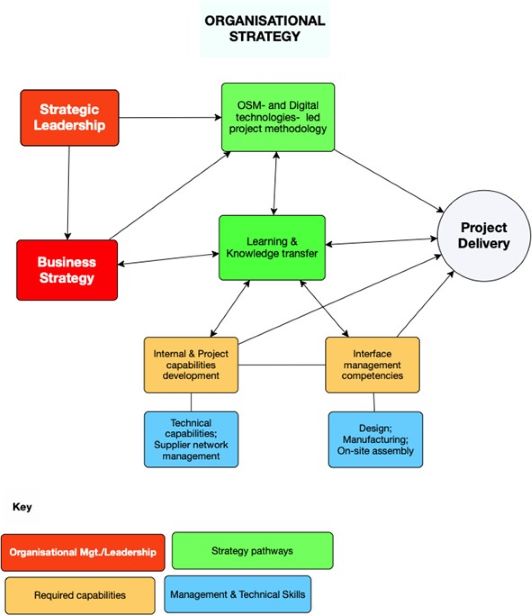
This is because, as design and build contractors, they find themselves operating as integrators and design coordinators for OSM projects on which clients nominate (specialist) consultants (e.g. for structural, mechanical, electrical and plumbing, laboratory or ventilation designs).
Beyond an understanding of technical issues (e.g. design tolerances, designing for transportation and hoisting skills), the skills needed to effectively manage multiple actors for projects (e.g. negotiation and emotional intelligence) are deemed critical by the team lead and the CE in delivering manufacturing approaches- and digital technology-driven projects.
Digital technologies vs human-centric management
Achieving the aim of transforming the construction industry based on the ambitious targets set out in the recent industrial strategy requires changes at organisational levels.
The journey towards widespread changes with manufacturing approaches, digital technologies and whole-life asset performance considerations at the forefront entails construction firms taking steps to implement their own transformation plans.
Beyond the acquisition of technical elements such as BIM software and setting up equipment for manufacturing, the example described in this post highlights the importance of human-centric management-oriented capabilities.
For construction firms to venture into and remain competitive in the delivery of projects using innovative manufacturing approaches and digital technologies, the latter remains a critical element for a successful transition.
From the case of DBC discussed, drawing up and implementing a clear strategy is crucial. Committed leadership and management, a clear business strategy and the development of relevant internal and project capabilities are key elements for a successful transition.
Implementing a plan to ensure continuous cross-project learning and intra-organisational knowledge transfer is critical for refining the overall strategy and informing leadership decisions for the future of the transition journey while remaining competitive in the construction market.
Dr Kwadwo Oti-Sarpong
Senior research and teaching associate in urban systems and infrastructure management
Cambridge Centre for Smart Infrastructure & Construction
www-smartinfrastructure.eng.cam.ac.uk