At a time when housing is so desperately needed and demand far outweighs the supply, Modern Methods of Construction (MMC) could be the answer to deliver homes quickly, sustainably, and in volume, explains Saint-Gobain Off-Site Solutions
Let’s look back to 2019, when the UK Government introduced the Future Homes Standard as part of a broader plan to reduce carbon emissions, with the ambition to reach net zero carbon emissions by 2050.
The Future Homes Standard, which will take effect in 2025, sets out that all new homes should produce up to 80% less carbon than homes built to Approved Document L 2013.
For Saint-Gobain Off-Site Solutions, harnessing innovative technologies and a deep understanding of how MMC and off-site construction can be used to meet these ever-evolving housing and environmental challenges is a key focus.
Discussing this further, Will Frost, head of housing solutions at Saint-Gobain Off-Site Solutions, and Tom Cox, construction solutions director at Saint-Gobain UK & Ireland, delve into the benefits of implementing MMC from the outset to meet and even exceed the Future Homes Standard requirements.
Introducing MMC in the early stages
Firstly, we don’t necessarily need to innovate new products and features to meet the Future Homes Standard.
Instead, we should consider how and where MMC is applied in a project’s timeline and ensure it is implemented early enough for the project to feel the full benefit of off-site manufacturing.
Optimising construction from the outset of a project is crucial to building efficient, high-performing homes.
MMC and system-specific thinking are often only considered for a project at its technical design stage or even after it’s already in the construction phase.
By this point, the design is often too far developed to reverse-engineer it for optimal use of MMC, and much of its benefit will be lost.
Therefore, these modern methods of construction are applied in a sub-optimal way, and this limits the performance benefits and productivity improvements that can be achieved.
Year upon year, Homes England falls short of its affordable housing targets when MMC and off-site can help offer a solution. However, we must change the way it is implemented by ensuring it is factored in during the initial design phase.
It is vital that buildings are designed around core metrics that work for MMC, rather than trying to shoehorn systems into a traditional project delivery process.
The client should be considering the type of MMC they can use on their build from day one, so a brief for design can be prepared accordingly.
Looking beyond a box ticking exercise
While it’s important to put MMC at the forefront of the design process, it’s also important to consider the end-user. Conforming to the requirements shouldn’t be a box-ticking exercise.
We should think beyond the legislation and look to the end-user’s lifestyle and requirements, and how the property will be used over its life to gain the greatest benefit.
The Future Homes Standard is more than just a paper-based box ticking exercise and fuelling homes with carbon neutral energy sources, it’s also key to understand the balance between all aspects of the build and how they will work for the people who will eventually inhabit the new homes.
As an example, heating bills for the resident can differ based on whether heat is generated through electric panels rather than air source heat pumps, but also by using a better building fabric which reduces the energy demand in the first instance.
Understanding how the house will be used, and therefore how it may consume energy, vastly changes how you approach the building process.
This is not unique to off-site construction; it’s a mindset change that all who want to deliver high-performance housing need to make, whatever the materials used.
Always bringing it back to the customer
Saint-Gobain Off-Site Solutions uses a customer-centric approach to fully understand the customer’s expectations and the demand the end-user is likely to generate, to create a full understanding of their performance aspiration for the build.
In a cost-of-living crisis, it’s even more essential to consider how to reduce a dwelling’s running costs now and in the future, and this starts with the right specification.
This is achieved by not only considering the building fabric, but how this key information works and balances with other key design considerations to deliver client and end-user benefit.
Other key design factors include size, location, and orientation of the building; glazing specification, size, and positioning; and finally, the mechanical and electrical loads and method of delivery (which will change drastically following the introduction of the FHS).
Without considering all of this in a balanced design, clients are likely to experience issues in project delivery and a sub-optimal end product for their customers.
When considering something which is perceived to be simple like glazing, buyers typically consider whether the property lets in a sufficient amount of natural light, but designers have a number of conflicting design considerations they need to consider in order to achieve this without causing negative outcomes.
They have to balance the fabric performance to ensure the ratio of glazed and unglazed areas meet thermal regulations and how they are detailed to provide a uniformed fabric, understand the risk of overheating in warmer spells and benefits of solar gain at cooler times of the year, understand the regional and orientation impacts, and now more than ever consider how the specification will perform over the tenure of the building with expected climate change predictions.
It is too easy to become focused on easy-to-measure metrics such as a U-value. While achieving good U-values for all elements in a building is important, we should be looking not just at the fabric, but also what is added afterwards such as methods of power and heat, what the window’s impact will be, and how the roofing solution will affect the overall building performance.
Ensuring that the fabric is adaptable and yet is confirmed to perform as promised, with any changes the fabric may go through in the life of the building, is going to be key to the success of the Future Homes Standard. A good wall is a great start, but it’s not the full story.
Using learnings from eHome2 to build better homes
A priority is delivering high-performing, cost-effective homes at scale, and the renowned eHome2 project can help us learn more about how to do this.
The pioneering project saw the construction of a three-bedroom family home take place inside of the world-leading Energy House 2.0 climatic chamber facility at the University of Salford.
eHome2 is a collaborative partnership between housebuilder Barratt Developments, Saint-Gobain UK & Ireland, and Salford University, built using a combination of off-site, modern construction methods.
The facility’s ongoing testing examines how we can erect buildings quickly and in volume using optimised construction while also meeting or exceeding the Future Homes Standard.
We’ve seen a positive output from baseline testing, which achieved within 3.8% of the thermal design performance when measured at a whole-house level as it’s heat loss coefficient.
This is a huge step in the right direction, compared to studies testing whole-house performance between 6% and 140%.
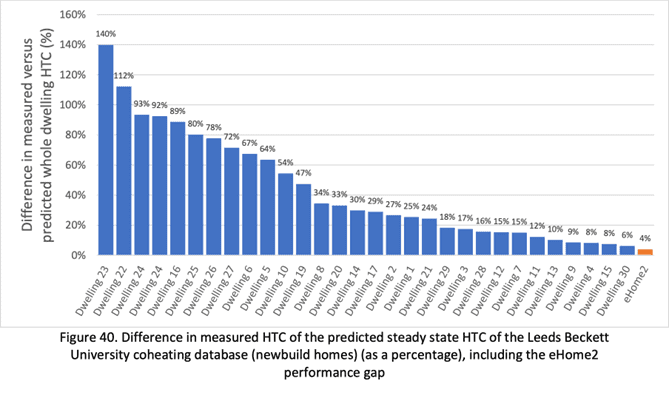
Even though a great house-level thermal performance was measured, we found areas that could be improved and are now implementing those through design and product change and factory process, controls, and systems.
This will enable us to deliver a quality product designed to customer and regulation requirements and delivered via an auditable, compliant process.
Another whole-house performance driver was the unit level air tightness. eHome2 was designed to achieve 3m2/m2/hr and when tested, it exceeded this by achieving 2.8m3/m2/hr.
Houses need to be designed, delivered, and commissioned by considering the house as a product, not a series of components.
The next phase of research in eHome2 is to understand how the different mechanical and electrical configurations, such as heating properties, affect the fabric.
Education and optimisation of MMC
The best results from innovation in housing can only be achieved if early design stages consider the use of MMC and off-site construction, and understanding how it fits with other key design considerations.
The aim is not just optimising the product for its delivery but optimising the design and integration of products to provide meaningful and consistent building level outputs.
We can ‘build’ a high-performance home on paper, or to spec in the latest tech, but bringing those buildings into reality with precision and consistency is the challenge that the Future Homes Standard sets us, and this is where the mindset within the industry need to change.
Additionally, there remains a lack of awareness around MMC. Not only the design but also the manufacture, logistics, installation, commissioning, use, and circular potential. To achieve a productive, sustainable, and commercially viable construction offer, awareness and the skill requirement required to deliver needs to be built.
With no real pre-qualification for contractors to install modern building systems, it’s very much a ‘learn on the job’ environment. A more structured training programme covering a range of solutions lends itself to a more educated build.
In turn, this leads to better quality and consistency, and this is an area that deserves more focus and consideration. Much of MMC continues to be misunderstood, but it can be resolved through more education, such as having supply chains interact with architectural faculties at universities to offer value-added training.
Only by educating and working with architects, contractors, suppliers and end users can we truly optimise MMC to start enhancing both public and privately delivered housing stock with high-quality, high performing homes that meet, or exceed, the Future Home Standard.
What happens next?
As the Future Homes Standard implementation date edges closer, we encourage key decision makers to keep MMC in mind from the very first stages, in order for new homes to be delivered quickly, safely and in volume while feeling the full benefits of optimised.