Digital construction tools can boost modular construction by enabling leaner production and the use of more sustainable materials, argues Ben Townsend, solution specialist at Graitec and Elitsa Yakimov
Construction projects that follow a circular business model design out waste and pollution from the early project stages through to a building’s end-of-life, intercepting the take-make-dispose linear pattern of production and resource consumption.
One Modern Method of Construction –modular – has shown potential to transform the industry and push the UK economy towards its target of net zero carbon emissions by 2050.
Thanks to its predestined characteristics for disassembly and reuse, modular construction can enable circularity by saving on resources, producing less waste and allowing a second life for products and materials, for example, insulated panels.
What is holding back building owners, architects, developers and contractors from sharing blueprints and resources to replicate successful modular projects?
The problem: A plethora of sustainable construction methods and materials, but not enough scalability
From an executive point of view, the costs of modular construction aren’t dramatically lower than when using traditional methods, which is an obvious deterrent.
From a planning perspective, project designs require repeatability and commitment. Project success, time savings and attendant cost benefits can be reaped only with full transparency and when all stakeholders are aligned at every stage.
Another demotivating factor can be project complexity; for example, when a variety of materials is required but design software for each lack interoperability.
The solution: Digital construction tools for assessment of the environmental impact of structural elements and construction materials
In the construction sector of the past decade, eco-goals used to be addressed mostly via the use of by-products in concrete production and recycled concrete, which generally represents a downcycling of materials.
However, with the increasing endorsement of timber-framed housing and structural insulated panels as alternative building materials, as well as resource-smart modular methods, the adoption of circularity principles in the construction sector is widening its scope.
Today’s materials range from limecrete to green steel, which means that there are few roadmaps for working with them and fewer still for calculating their behaviour, for example in seismic regions.
New digital construction tools and technical services that enable leaner project design from the early stages through to handover have been in existence for the past decade but now is the time to embrace multi-material design software, which can guide the application of new materials with precision, especially within modular construction projects, where early data processing is paramount.
Digital tools, such as Advance Design by Graitec, can accelerate projects and ensure their sustainable output with models that combine steel, concrete, timber and brickwork.
Empowering architects and engineers to make environmentally conscious decisions
More importantly, Graitec’s Finite Element Method (FEM) software features a CO2 emissions calculator for precise carbon factor measurements for construction materials and elements during the early stages of design.
Equipping architects and engineers with graphical results and informative reports, it empowers them to make environmentally conscious decisions about all structural engineering aspects of their designs. Further supporting circularity, this software is BIM-compatible and provides 3D fine elements analysis, all in one package.
Another new tool by Autodesk, Forma, features a suite of sustainability solutions that enable architects, real estate developers and urban planners to better understand the implications of their design decisions at the onset of projects.
By using data-driven insights and visualising the impacts of their design decisions in real-time, on a host of environmental factors, teams can deliver smarter, more sustainable projects.
Circular Business Models (CBMs) for Modern Methods of Construction
Applying a Circularity Business Model to construction projects may mean challenging current processes, product choices and concepts. Here, digital modelling can justify the choice of novel materials, such as the application of cross-laminated timber (CLT).
For example, the inbuilt strength of CLT would allow for the removal of lintels in openings and steel in cantilevers when used correctly. Practices such as this push back on the pressure “to stick with what we know and have always done”. Utilising a digital model for decision-making will not only generate competitive advantages but also enable the use of sustainable building methods and materials.
The use of digital design enables value engineering, which provides the optimum solution rather than the typical solution. For example, a digital design model can illustrate the project benefits of using a glulam beam instead of steel, or how we can minimise the concrete requirement of the foundation slab.
Structural engineering software such as Advance Design facilitates this through finite element analysis, allowing us to specify the minimal materials required, as well as understand the materials better.
Government incentives must be enforced to support Circular Business Models
Since the benefits of using Modern Methods of Construction aren’t immediately obvious, the right government incentives must be put in place to support Circular Business Models.
The 10% green requirement currently in planning, SAP ratings and the Net Zero mandate for new builds don’t manifest as modular construction as often as they could, because of profit and other compromises from developer level down to the supply chain.
In addition, educating and incentivising stakeholders can be supported not only through policy frameworks that promote sustainable public procurement practices but also through concrete examples from lighthouse projects and digital twins.
For example, one of the oft-cited issues with modular construction is the loss of project control since most work is being outsourced offsite. This can be prevented with tighter controls and full transparency during the design phase and training labourers during
the construction phase – practices that modern digital tools make easy to implement and understand.
This will, in turn, lead to quicker and more efficient build processes, leaner infrastructure and healthier homes, and sustainable solutions at end-of-lifecycle, all of which represent a standard, replicable circular business model.
Scaling-up modular projects for more sustainable construction: A holistic approach to construction by means of digital roadmaps
A holistic approach to modular construction must eliminate budget compromises and provide team education from the early design stages, ensuring their commitment through to handover.
The roadmap for such an approach can come from existing success stories. Projects that illustrate the advantages of circularity principles over the entire building lifecycle, from a sustainable digital design model to non-destructive product dismantling and interchangeability will further promote stakeholder buy-in and widen the adoption of Modern Methods of Construction.
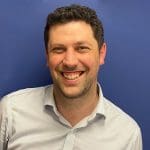
Ben Townsend
Solution Specialist
Tel: 07507849898
*Please note: This is a commercial profile.