Build Warranty explores the role prefabricated modular housing has in delivering greener, better, faster homes as part of the UK government’s target of building 300,000 new homes annually by 2025
According to recent data, new home registrations increased by 25% in the first quarter of 2022; a total of 45,991 new homes were built, compared to 36,665 in last year’s first three months. However, the UK is still facing a housing crisis, leaving a substantial gap to bridge.
With the UK facing various pressures too high quality, cheaper, and more sustainable homes, many advocates within the industry have – touted the answer to the UK’s housing crisis – so far, a sector that produced very few homes. However, the problem is not new; back in 2013, the UK government published its strategy Construction 2025 plan, which set out ambitious targets for lower costs (down 33%) and emissions (50%), plus faster delivery, cheaper, safer, and greener housing.
There is an ever-increasing move away from traditional ‘bricks and mortar’ construction methods and guiding towards Modern Methods of Construction (MMC) to find innovative solutions. And whilst MMC is used to encapsulate different methodologies, undoubtedly, one at the forefront in potentially meeting those sustainable targets is Modular Construction.
There are many types of MMC, but one popular sub-methodology of Modular is a system called Volumetric Modulars, whereby a significant proportion of the assembly of the building parts is built off-site in factories and transported on-site. Once assembled, these “modules” or “pods” are connected and stacked, usually attached to a frame or podium, on top of pre-cast concrete foundations.
A method that received universal acclaim for bringing much-needed NHS Nightingale facilities onstream in record time over the past two years during the lockdown period, shining a light on the modular sector and initiating a shift towards modular technology, which has noticeably gained admiration in the construction industry.
What are the benefits of prefabricated modular housing?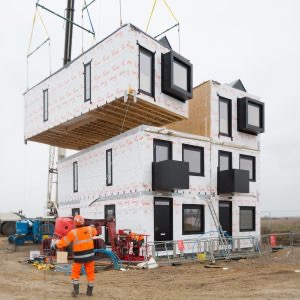
For the UK to meet those net carbon zero by 2050, adapting modular technology to the frontline can be less energy efficient and fast-produced in manufacturing. Although production and assembly vary, the average completion of construction usually can take around 16 weeks. This is because on-site substructure and infrastructure can occur whilst the superstructure is being built offsite. Projects can be completed 30% to 50% sooner than traditional construction.
As for environmental benefits, one of the greatest benefits of prefabricated modular homes is waste control. A DEFRA report highlighted that in 2018, construction, demolition and excavation accounted for 62% of the UK’s total waste as Modular homes are prefabricated off-site in factories according to specific measurements. As the material is cut to shape by digital technology, there’s no need for excessive material, which reduces waste on site significantly.
And another large benefit to using modular is the less impact on climate change and transportive output. Prefabricated modular designs see a 40% reduction in HGV movement at construction sites, and manufacturing off-site minimises the time and energy spent on site. This cuts travel and transport, as workers are more likely to be concentrated around a specific factory. Due to these factors, overall pollution is reduced.
How can we overcome the barriers to greener homes?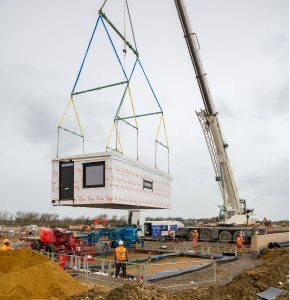
For greener, faster, cheaper, and better homes, governments must enhance sustainability by introducing a more robust commitment to housing targets by removing barriers and fast-track planning for more prefabricated modular homes.
The housing sector has for decades lagged other sectors in reducing carbon emissions; according to the governments, housing emissions were cut by 1 million tonnes of CO2 equivalent from 2018 to 2019 compared with cuts of 8.5 million tonnes from energy supply. The government seeks to decarbonise the industry in line with net zero. Still, to meet those targets, record spending In Research and Development must be considered across the whole construction sector. This investment could deliver even more energy-efficient homes.
Steve Cole, director of Make UK Modular, the trade body for modular housing, said: “There is a housing success story in this country, and it is modular. This report shows definitively that modular is now a significant player in the UK housing market. Government must capitalise on this as opportunities to transform our broken housing market into the most sophisticated in the world do not come around every day.
“Government must accelerate modular delivery, building on the investment made and the jobs created, by removing the remaining barriers holding the industry back.”
Additionally, the construction industry has a bigger opportunity to meet growing demands by becoming both product and supply driven — both possible through modular construction.
Three points must be considered for the industry to meet those growing needs.
-
Increased productivity through automation and technology
The UK faces a shortage of construction skills as younger workers choose alternative professions. Modular construction can help bridge that gap. With substantial investment, the industry has pledged those 40 new factories in post-industrial towns and cities. The modules can be manufactured in factories with efficient automated processes, thereby enabling high volumes of quality products to be delivered at speed.
-
Drive technological and creative careers through new apprenticeship programs
With increased MMC factories across the UK, large amounts of employment prospects are needed not just to drive the production line of modules. An estimated 3,000 + new jobs could be created for MMC to reach scale, including digital manufacturing, engineering, and design. To attract people to the industry, apprenticeship business models will be needed to adapt, including integrating new tools and technologies, such as building information modelling.
-
Effective partnerships
In 2019, Japan’s biggest MMC homebuilder, Sekisui House, announced its move into the UK housing market after striking a deal worth £90 million. The deal will see it work in partnership with Homes England and Urban Splash to deliver thousands of new homes across the country. A partnership like this already has £22 million of new equity; through the Home Building Fund, Homes England is investing another £30 million of equity and debt funding. An investment like this could drive manufacturers, construction organisations, and developers to deliver modular products at scale.
What are the key challenges of prefabricated modular homes?
This is a growth market, and there are challenges, as there are with every construction project, and they do require a different approach to traditional construction methods. Insurers are still wary of modular construction, as generally there isn’t enough yet built up in the UK, and lack of data to see how these buildings perform over time to have reliable actual models.
The other biggest challenge to MMC buildings is the risk of a fire. Especially when insulating materials are exposed until the exterior and interior of the property are enclosed. And even after construction, there is still a risk of fire, and its important insurers and contractors work together to truly understand the make-up of the building to ensure it is insured correctly.
Here at Build Warranty, we specialise in all kinds of structural warranties, providing protection for homeowners to developers; we are the UK’s number one choice for warranty solutions, professional advice, and personal service. If you would like more information about our building warranties and how they could protect your building, we can guide you with the right advice.
Give us a call on 0800 5200155 to speak to one of our professional team, or email your enquires to us at info@buildwarranty.co.uk, and we will get back to you immediately.
Alternatively, you can complete a simple online form, and our team will process a price indication immediately: https://buildwarranty.powerappsportals.com/ldi-application/
Econpmies of scale may be realized by standardizing utility systems.Composite electrical wall bands may be used in all rooms. Drop in bathroom systems may be standardized. Heat and cooling pods may be xtandardized. inyerchangable room pods may be added or subtracted as family needs change. Pods may attach to a residence core assembly. Composite foundations may become an integral part of wall assemblies.
The biggest challenge is the cost of development , over heads, cash flow and the fact the business model does not work. On top of that the public have not accepted of site concstruction is better than trad.
This a VHS v Betamax problem (for those that are old enough to remember)