Offsite manufacturer, ilke Homes has delivered nine zero-carbon modular homes for SME developer Positive Homes
All nine modular homes have an Energy Performance Certificate (EPC) rating of ‘A’. In the UK, only 1% of new builds are ‘A’ rated, whilst 0.16% of total housing stock has this top classification.
The homes were manufactured by ilke Homes at its factory in Knaresborough, North Yorkshire and were delivered to Positive Homes’ site in Newark, Nottinghamshire.
Once onsite, the homes were installed onto pre-prepared screw pile foundations. Screw piling involves winding a steel screw-like structure down into the ground like a screw into wood. Unlike conventional foundations which require large amounts of concrete, screw piling involves digging small sections where anchors are lowered into and filled with concrete. By reducing the need for extensive ground excavation and large quantities of concrete, developers can speed up installation times while also cutting their carbon footprint.
Zero-carbon homes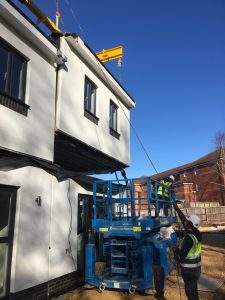
Increasing the supply of zero-carbon homes in the UK will be crucial to reducing the industry’s carbon emissions, with the built environment contributing around 40% of the UK’s total carbon footprint, according to the UK Green Building Council.
By manufacturing offsite, the modular homes are delivered in half the time of traditional methods meaning income streams can be accessed faster by private developers, housing associations and local authorities.
Positive Homes is a sustainability-focused developer, building energy efficient, sensibly priced homes.
Home Building Fund
It has recently received £750,000 grant from Homes England through its Home Building Fund.
The Home Building Fund offers funding to the SME developer market as the government looks to support marginal sectors to rapidly increase the number of homes being built. The government has set a target of building 300,000 new homes a year, but current build rates fall short by over 100,000.
Switch to offsite manufacturing
Dave Sheridan, executive chairman at ilke Homes, said: “Given the enormity of the climate change challenge, it is crucial that as an industry we make determined efforts to shift towards a far-more sustainable approach.
“Offsite manufacturing consumes considerably less energy than traditional construction methods, and is the most efficient method of delivering high-quality and highly-sustainable homes at speed.
“If we are to get serious about tackling the climate crisis, then offsite manufacturing will have to play a much bigger role. At present, far too many new builds are failing in terms of their energy efficiency.
“By switching to offsite manufacturing, we can quickly deliver the zero-carbon homes of the future. We’re proud to be working alongside Positive Homes, and leading the way in delivering the very best and most sustainable homes on the market.”
Martin Valentine, managing director at Positive Homes, added: “SME housebuilders must play a pivotal role in tackling the UK’s housing shortages if the government and industry is going to face the challenge head on. Homes England’s accelerated access to funding and direct assistance to SMEs builders will continue to allow developers, such as ourselves, to deliver sustainable homes at speed across Britain.
“Improving SMEs access to land and finance will also have far-reaching benefits in local communities as employment opportunities increase while also supporting supply chains.”