The UK’s construction industry is seemingly on the cusp of crisis point, with many different factors causing projects to slow and impact efficiency. Vincent Matthews, marketing manager at SFS, discusses how fasteners and fixings can raise productivity once again and help keep construction work on track
The challenges faced by the construction industry are widely acknowledged. Even though construction contributed £113bn to the UK economy in 2017, according to research from Parliament UK, it is impacted by many different issues, and there could be even more difficult times ahead.
One of the biggest issues for construction is poor productivity. Common factors that lead into this are delays in equipment being delivered to site, poor weather, not ordering enough materials, and not specifying the right product from suppliers.
Further hampering productivity is the ongoing skills shortage. According to the Chartered Institute of Building (CIOB), the UK needs to find 157,000 new recruits by 2021 in order to keep up with demand. Brexit is set to compound this issue even more. With a lack of available labour to fulfil the work, projects are falling behind, and costs are going up.
Then there’s the digital transformation being imposed on all layers of construction, through the likes of government schemes like Digital Britain and the need to work smarter with new technology. The initiative aims to transform how construction comes together, placing more emphasis on BIM (building information modelling).
This isn’t a slow-moving beast either, and the use of BIM has progressed rapidly. From 3D BIM (sharing graphical and non-graphical information digitally), through to 4D BIM (which adds time-related scheduling data), 8D BIM is now emerging.
While the intention is for the greater good, implementation is far from perfect, with architects and specifiers relying on BIM-enabled manufacturers. Suppliers are also racing to provide BIM information to their entire back catalogue of products – a task that is much easier said than done.
While the future may sometimes seem unpromising, and the answers to these ‘big picture’ challenges are not immediately clear, there are different methods of speeding up construction. One key aspect is through the specification and use of fixings, fasteners and the products used on site.
Faster fixings, engineered for efficiency
Fasteners and fixings are arguably seen by many as one of the most unremarkable components of a construction project. Most will view them as simply a means to an end of fixing down other larger materials, the fashionable products like floors, walls, ceilings and panels. The ‘showpieces’ of construction materials, so to speak.
Yet, with hundreds upon thousands used every day on construction sites around the nation, they really are the ‘everyday hero’. Cleverly engineered fixings can yield efficiencies that are somewhat hidden to the naked eye and often aren’t considered.
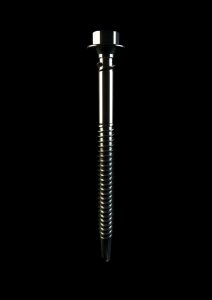
Take, for instance, the SXC5 fastener, one of the latest generations of self-drilling composite fasteners from SFS. The tip of the fixing itself has been re-engineered to have an optimised tip geometry that helps with easy setting, enabling installers to drive the fixing into the material they are fixing onto quicker.
Fixings are also commonly subjected to ‘overdriving’. This is when the fixings are overtightened, causing damage to the substrate, as well as the fixing itself. Once this happens, it can compromise whole sections of the building fabric, and ultimately may need removal and replacement, adding on capital costs, labour time and money.
However, there are easy ways to prevent this scenario through the right fasteners. The SDK fastener, for example, is another self-drilling fastener that has a unique design. It features a square drive that is held in a special drive bar. When the fastener reaches a pre-determined torque the peg snaps-off, ensuring the fastener is installed correctly.
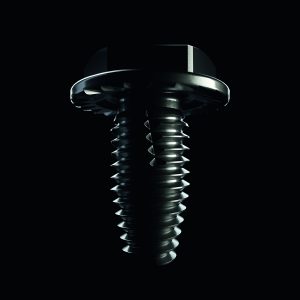
Another innovative fastener from SFS is the TDBL. This self-threading fastener can be inserted into punched holes to fix thin to thick metal structures together, and is highly suitable for awkward areas such as box sections and ‘blind’ fixings. Until the TDBL, putting pre-drilled supports together was a time-consuming task, requiring standard bolts, washers and nuts, with accessibility required from both sides, which is not always possible. In extreme cases, this can lead to the project needing to be taken back to the structural engineering stage, incurring huge costs.
There are many more unique ways in which fasteners can speed up the process for installers when they are on site. Crucially, to get optimised fastener performance, it is imperative that the industry at all levels are involved in new product development to help solve common challenges.
Less is more
It’s not just innovation in the way fixings are designed that can produce efficiencies. Building support frames, like cladding and rainscreen brackets, have also evolved to make installation more economical in time and labour, and are further supported by online tools such as NVELOPE’s Project Builder, which can help with project and material calculations for building envelopes.
Another great example is the flat roofing fixing solution for fall protection systems like the Soter II Horizontal Lifeline system. When fixing these systems to roofs, gravity toggles have been the industry standard, but installation can sometimes be tricky. The toggles can sometimes become entangled in insulation or temperamental when deploying the anchor to secure the system to the flat roof. Now though, manufacturers are offering a sleeve fastener option. Indeed, the Soter II system can be secured using just eight sleeve fasteners, which is a much simpler and quicker method.
Fasteners for every application
With fasteners, there should never be a one-size-fits-all approach. Each application will be different, and to realise efficiencies during the installation processes and to minimise failures, there needs to be careful selection of the materials used.
For more about SFS, please visit www.sfsintec.co.uk.
Vincent Matthews
Marketing Manager
SFS Group Fastening Technology Ltd
Tel: +44 (0)113 2085 500
Please note: this is a commercial profile.