Modern Methods of Construction and offsite are far from new, with firms across the globe recognising and embracing its many benefits. Lorraine McMorrow, head of digital at McAvoy, explores what’s next for digital in offsite manufacturing
Offsite manufacturing has been a game-changer for an industry that has been notoriously slow to modernise. Its adoption over the past few years has been accelerated by the imminent need for efficient construction across the UK, with offsite proving a fitting answer to many of the quality, sustainability and speed challenges faced by the sector.
2022 saw firms face unprecedented pressures caused by the well-documented global skills and people shortage paired with increased material costs, which exposed the painful vulnerability of the construction sector as a whole. It was also a year of shifting perspectives as companies right across the world began to embrace the benefits of digital technologies which have been a true game-changer for the industry.
Digital construction has an important role to play in the industry
As we look towards the year ahead and even beyond, there is no denying that digital technology will have an important role to play in the construction industry. We are already seeing it increase project visibility and transparency due to its easy access to analytics and data, creating a much more collaborative process between all parties involved in the built environment process.
Of course, that requires all stakeholders buying into the idea and embracing it. Only then will it be a truly collaborative process which provides an opportunity for even-better decision-making while reducing project risk.
In 2023, we can expect technology to push design capabilities to new heights, providing architects and manufacturers with opportunities to create new and innovative design possibilities while drastically improving speed, quality and accuracy of the build.
Offsite manufacturing can provide a solution for buildings in both the public and private sectors
With an increased demand for schools, hospitals and residential builds – coupled with the government’s ambitious CO2 emission targets – firms are being forced to rethink how they deliver. The argument for offsite manufacturing providing a solution to this crisis is now stronger than ever, with its reduced reliance on a diminished trade-based skills pool, its versatility and its undeniable eco credentials.
Many have become somewhat comfortable with the use of Building Information Management (BIM) systems that enable firms to bring ideas that previously could only have been conceptualised to life through ground-breaking digital innovations. As an industry, we need to view BIM as a process of information management used in line with the myriad of technologies to create efficiencies.
Automation can drive productivity
As we move into 2023, we can expect to see more firms driving up productivities by automating tasks. Smart analytics from project information will enable firms to make more accurate decisions based on real-time data. The management of this information will in turn create a more productive sector as a whole as firms create better ways of designing and manufacturing buildings – reducing costs in the process while simultaneously creating a safer working environment.
The construction industry is renowned for its ‘find and fix’ model, which has seen firms face expensive delays for decades. Firms can now leverage digital technology to access project data and identify and rectify any potential issues before they even become a problem, enabling them to improve processes, build capabilities, value and reduce build time.
Those who have been slow to utilise digital technology, relying instead on the ‘wait and see’ approach, may be persuaded to introduce digital processes and technology into their business as the new Building Safety Bill, which rolls out later this year, sees developers and clients taking more responsibility for building safety compliance. All accountable persons will be required to prove their own due diligence, which can only be done through digitalisation, which will enable them to maintain a golden thread of information for each building or asset.
Digital twins are the next step for digital construction
The next step for digital construction is a drive towards digital twins with realised real-time projects modelled and monitored in a digital environment. This certainly has its perks, particularly for complex projects, with smart sensors and analytics successfully enabling stakeholders to access real-time information management at all stages of the build. Although this concept of digital twins has hung around the wings for a long time, it would appear it is finally making its mark as it begins to drive design conversations throughout the industry.
As we look towards the worksite of tomorrow, there is no denying that digital technology promises to deliver a big impact. At McAvoy, we have embraced the power of digital technology across our business. We already use augmented and virtual reality alongside BIM and Information Management to ensure projects are delivered more effectively and efficiently and as we get ready to launch our new digital strategy this year, we look forward to harnessing this even further.
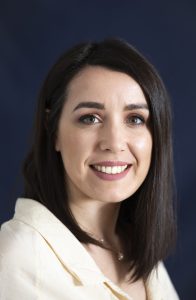
Lorraine McMorrow
Head of digital
Tel: +44 (0) 28 8774 0372