The construction industry and our ability to “build, build, build” is key to the UK’s economic recovery. Martyn Holloway, business development manager – flat roof at SFS, discusses how innovative fastening solutions can lead to fast and reliable single-ply flat roofing installations
Covid-19 has put the world on pause – and the construction industry, in particular, has been hit hard, with 680,000 employees on furlough at one point.
Of course, the government recognises this cannot continue. The rhetoric is “build, build, build” to get the construction industry, and the UK economy, on the road to recovery. It is vital, though, that we can turn this rally cry into practical measures for those on the frontline of construction – our contractors and installers.
Solving an age-old challenge: Speed of installation
Site productivity is one element that is more important than ever. This is needed specifically to help with offset delays following the introduction of site operating procedures as a consequence of the Covid-19 pandemic. Also, with autumn and winter coming, there are more traditional delays such as extreme weather conditions to contend with.
Then there’s the challenge of the shortage of skilled labour, which has been exacerbated by a heavily furloughed workforce. This, combined with an ageing workforce, means there is a real need to train new site operatives.
Amendments to existing Building Regulations, guidance documents and operating procedures are adding complexity to the industry, which in turn is increasing time pressure on site. Then there’s the intricacies of installation itself that installers must deal with.
Tapered insulation challenges
One such example is ‘cut to fall’ insulation systems. Growing in popularity for new build projects, these can be particularly challenging for installers.
Also known as tapered roof insulation, the aim of this fastener system is simply to provide drainage when the roof deck itself does not provide adequate falls. This is achieved by increasing the thickness of the insulation to provide the slope and run off for the rainwater.
However, when using a conventional mechanical fixing solution to install the insulation, there is typically a myriad of different fastener lengths needed to allow for the change in insulation thickness. In turn, this increases the complexity and time on the job for roofers.
Concrete deck challenges
If ‘cut to fall’ insulation is being secured to a concrete deck, this can also slow down installation. Using conventional flat roofing fasteners may require pilot holes up to 100mm deep in order to rationalise fastener lengths, significantly adding to the drilling time.
Adhesive system complications
One of the biggest challenges for installers is if they are using an adhesive system to secure the membrane and insulation layers. Weather conditions on the day can severely hamper progress, and the design is limited by a specified maximum wind load. Additional time is required to prime the deck and adhere each separate layer, including the Air and Vapour Control Layer (AVCL), insulation and membrane.
Adhesive systems also rely heavily on the skill of the installer to apply the correct weight of adhesive bonding agent per square metre for each of the AVCL, insulation, membrane and other layers required. If not secured correctly, the membrane will need to be reinstalled, adding unnecessary time on to the job.
Retrofit risks and difficulties
Another area where installers can hit snags is on retrofit roofing installations. Here, roofers will often face existing layers of membrane and insulation. These are typically overlaid with new membrane and insulation layers. However, using adhesive to attach these new layers and by not securing existing and ageing layers, this risks potential failure of the roof.
Additionally, new or existing cut to fall systems or existing tapered screed layers will lead to a variation in the build up at any single point. Installing traditional mechanical fastener systems therefore requires installers to use a variety of fastener lengths across the roof, adding significant time and complexity to the install.
Making haste with mechanical fixings
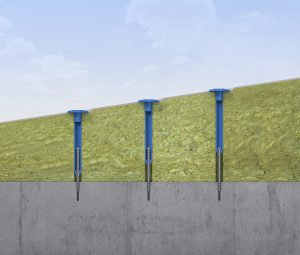
These challenges can all be overcome with innovative mechanical fixings, which can securely fix every layer of the roof, provide reliable performance and long-life warranties.
Compared with adhesive systems, mechanical fastening systems are less weather dependent, and can be used in all exposure zones. For refurbishment and new build concrete decks, pull out testing will assist in calculating the appropriate fastener design load. When used in conjunction with the project wind load calculation, the correct fixing pattern can be determined to ensure a safe and secure installation.
For tapered insulation challenges on concrete decks, installers can use the innovative TIA system from SFS. This height-adjustable insulation fastener solution is specifically designed to self-adjust to the insulation thickness, as the fastener engages with the telescopic sleeve and the result is a considerably simplified install.
Drilling time is greatly reduced using the TIA system too, as it requires just 35mm deep pilot holes for all settings. When compared to the conventional practice of drilling up to 100mm deep pilot holes for tapered schemes on concrete decks, this typically equates to 60% less drilling.
When the heat is on, use heat induction
A final area where contractors can speed up jobs is by using heat induction welding technology, such as the patented isoweld® system from SFS, to install singly ply membranes. Since its launch, more than 15m square metres of single-ply membrane has been successfully installed.
This technique uses electric heat induction to weld the membrane to a specially coated metal stress plate located underneath. The result is an extremely secure fix without penetrating the waterproof layer.
Each plate only requires three seconds to weld and the SFS isoweld® system is also easy to set up and calibrate. Suitable with both PIR, EPS and mineral wool insulation types, the heat induction technology can be used in conjunction with PVC, TPO and EPDM single-ply membranes.
The membrane fasteners are installed in field fix patterns in comparison to the traditional lap fixing and therefore significantly fewer fasteners are required. Typically, up to 50% fewer fasteners are required and the isoweld® field-fix system allows installers to use the widest membranes available, which substantially reduces the extent of seam-welding required.
The TIA fastener system can be used in conjunction with isoweld® to offer a faster and more cost-efficient install for concrete decks.
A secure roof, a secure future
Embracing new innovation opportunities such as TIA and isoweld® is critical if we are to recover quickly. By incorporating new roofing technologies, site productivity increases, roofers can be more efficient and profitability goes up.
SFS is doing all it can to help installers and contractors during these difficult times not just to secure roofs but to secure futures as well. From the provision of office and site support, through to maintaining the supply of product from our factories, we will continue to go that extra mile and provide the industry with assistance where required, including efficiency savings through product innovation.
For more about SFS, please visit www.sfsintec.co.uk.
SFS Intec
Tel: +44 113 2085 500
Please note: this is a commercial profile.